
長年楽しんできた、電子工作に関する小技やヒントを、書きつづって行きます。
1.ICピンの掃除 |
・古いICやLSIを出してきた時に、ICのピンが酸化膜で真っ黒けになっていたことはありませんか?
こんな時は、カッターで削る? スチール・ウール? 接点復活剤?
私は、消しゴムで消します! 普通のプラスティック消しゴムでOKです。
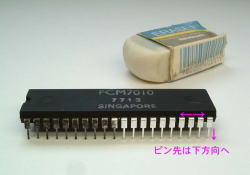 |
ICのピンを、万力等に沿わせて曲がらない様にし、消しゴムで軽くこすります。
写真の右半分だけを消しました。 ピカピカです!
くれぐれも、足の折れ曲がりと、静電気には注意して下さい。 |
|
2.愛用のハンダとハンダ付け |
・電子工作の必需品であるハンダにも、太さ、成分、ヤニの含有などで、色々な種類があります。
私が30年来、愛用しているのが、日本アルミット社製 「アルミット」 KR-19 60Aの0.8mmです。
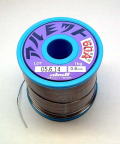 |
このハンダは、スペースシャトルに使われたり、MIL(ミル)規格も取得している、優れもの?です。
非塩素系のヤニですが、酸化膜の除去にも優れ、ハンダの流れもスムーズです。
値段は高めで、写真の1Kgで8,000円ほどします。 |
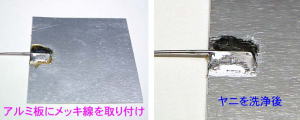 |
何と言っても、その名の通り、アルミにハンダ付けできてしまうのが驚きです。
アルミ板は、アルマイト加工がされているので、表面をカッターで削り落とし、スズメッキ線を付けてみました。 |
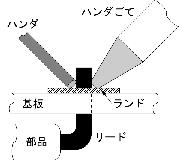 |
ここで、少しハンダ付けのおさらいです。
図のように、ハンダごての先で、部品のリード線と基板のランドを温めて、熱せられたリード線とランド側にハンダを接触させるのが良い方法とされています。 こうすると、ハンダがきれいに流れて、張りと艶のある仕上がりになります。
趣味の製作とはいえ、基本を守ることで、上達につながると思います。 きれいに仕上がった作品は、愛着がわきますね! |
|
3.ハンダごて と ポンプ |
・昔のハンダごてはニクロム線だったので、こて先が重く長時間の作業で腕が疲れましたが、
セラミック・ヒーターが登場したおかげで、作業がずいぶん楽になりました。
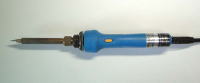 |
私が現在使用しているコテは、gootのTQ-95、先径1mm丸型で、通常時15W、スイッチを押すと90Wに加熱できるタイプです。
先端の形は好みがありますが、温度が変えられるコテは大変便利です。 |
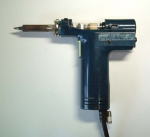
|
ハンダ吸い取りポンプは、値段が高いこともあり、アマチュアで持っている方も少ないかもしれませんが、部品取りだけではなく、通常の製作作業にも大変便利な道具なので、購入をお勧めします。
写真のポンプは、10年以上前に約25,000円で購入し、5年前に内部のパッキンが劣化したので10,000円で修理しましたが、まだ現役で使用しています。
|
|
4.便利な治具 |
・普段使用しているペンチやニッパなどでも、十分に工作はできますが、ワンランク上の仕上がりと、便利さを求めるならば、専用に考案された治具は大変重宝します。
・リードベンダー
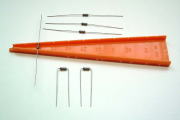 |
抵抗やダイオード、そしてジャンパー線などを基板に取り付ける際に、部品のリードを2.54mm間隔に折り曲げるための治具です。
ピンセットやペンチでは、どうしても間隔が揃いにくいですが、これを使えば、等間隔できれいな折り曲げ加工ができます。
抵抗を基板から浮かせる、フォーミング加工も簡単にできます。
|
・ヒートクリップ
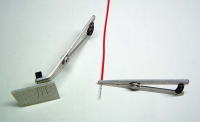 |
熱に弱い部品や、リード線の予備ハンダを行う際に、このヒートクリップを挟んでおけば、クリップから先に熱が伝わりにくくなり、部品や被覆を保護できます。
簡単な原理なのですが、大変重宝する治具です。
特にリード線は、被覆内にハンダが流れ込むと、折り曲げ時や、コネクターの抜き差し時の金属疲労が増しますので、注意しましょう!
|
・ICピンそろった
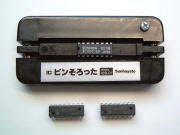 |
新品のDIP-ICは、たいていピンが縦方向に2.54mmピッチよりも広がっており、そのままでは基板やICソケットに刺さらないため、折り曲げる必要があります。
また、保存中に足が曲がってしまったり、不揃いになっている場合にも刺さりにくいと思います。
こんなとき、「ICピンそろった」を使用すると、簡単にピンをそろえてくれます。
表側では16ピンや20ピン等、裏側では28ピンや40ピン等のICも加工できます。
|
・DIP-IC引抜工具
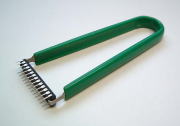 |
ICソケットからICを外す際に、ドライバーやピンセットで浮かせると、ICや基板に傷が付いたり、ICのピンが曲がってしまったりします。
IC引抜工具は、垂直にICを引き抜くので、傷やピンの曲がりを防ぐことができます。
性能により、価格帯に開きがありますが、使用頻度が少なければ、安いもので十分間に合います。
|
|
5.便利な工具 |
・治具と共に、電子工作用の工具にも、便利な物があります。
・ミニバイス(ヤンキーバイス)
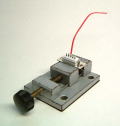 |
コネクターにワイヤーをハンダ付けする場合などに、卓上で部品を固定する際の必需品です。
万力では大きすぎる部品や、ちょっと固定したい場合に、手軽に使えます。
|
・ヘルピングハンズ
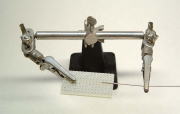
|
ハンダとハンダごてで、両手がふさがる場合に、基板や部品を固定する「第3の手」と呼ばれる道具です。
部品のリードに、ワイヤーを取り付ける際にも重宝します。
|
|
6.基板への部品取り付け |
・プリント基板やユニバーサル基板に部品を取り付ける場合、背の低い部品から順番に行うのがセオリーですが、縦型電解コンデンサ等を付け始めると、基板が傾いたり、ハンダ付けの瞬間に動いてしまい、作業がしにくくなります。
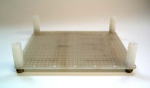
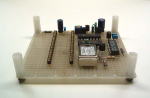
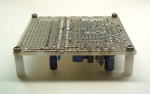 |
こんな時、たいていの基板には、四隅に取り付け用のネジ穴が空いていると思いますので、作業前に、この穴に一番背の高い部品よりも少し長めの6角スペーサーを、部品面に取り付けてから作業します。
これで、最後まで基板が水平に保たれるので、ハンダ付けが正確に行えます。
また、机面との擦れによる、部品の傷も防げます。
基板を裏返した際に、部品が落ちてしまう場合は、スポンジやタオルを小さくたたみ、その上で仮付けをして、部品の位置や傾きを整えてから、ハンダ付けすると良いでしょう。 |
|
7.部品の高さ調整 |
・LED(発光ダイオード)やセンサーを並べて取り付ける場合、高さを合わせるのはなかなか大変です。
・専用のスペーサーもありますが、LED本体と同じ様な価格です。
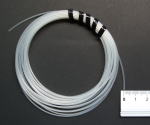
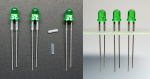 |
そこで、イラックスチューブ0.7mmを、任意の長さに切断し、
部品の足に通しておくと、高さ調整がしやすくなります。
トランジスタやセンサーも同様に設置できます。
|
|
8.すずメッキ線のハンダ付け |
・ユニバーサル基板で回路を組む場合、電源ラインなどを、ハンダ面にすずメッキ線で配線することがあります。
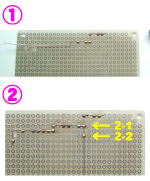
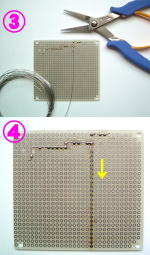 |
すずメッキ線をハンダ付けする際に、始点を付けた後に、終点を付けてしまうと、中間をハンダ付けする際に、熱によりメッキ線が膨張し、ゆがみが出てしまいます。
これを避けるためには、始点から順番にハンダ付けして行けばよいのですが、始点を付けた後、次のランドにハンダを付けると、その熱により始点のハンダも溶けてしまい、メッキ線が外れてしまいます。
こんな時は、始点を付けた後に、ランドを1つ空けて、3つめのランドからハンダを付けて行くことで、始点に熱が伝わりにくくなるので、メッキ線が外れなくなります。
メッキ線が浮かないように、おもり等で押さえながら、順番にハンダ付けを進めてゆくと、真っ直ぐに仕上がります。
最後に、残してあった始点の次のランドを付けて完成です。
|
|
9.基板のワイヤー配線 |
・電子工作関連のHPを見ていると、ユニバーサル基板のハンダ面で、配線をされている方を見かけます。
・この、ハンダ面での配線のメリットは良くわかりませんが、本来ハンダ面は、はんだフロー槽などの様に、熱を加える面なので、この面への耐熱性の無い部品配置や配線は、私はあまりお勧めできません。
また、下記のような弊害が出る恐れもあります。
・ 他の場所へのハンダ付けの熱で、配線済みの被覆が溶けてショートする。
・ ワイヤーを部品の足に固定しにくいため、ハンダ付けが難しい。
・ ICピン等の、とがった部分にワイヤーが刺さり、ショートする。
・ ワイヤーの下になった部分の、ハンダブリッジやハンダ不良が発見しにくい。
・ 一度配線してしまうと、配線ミス時の取り外しや、メッキ線部分の修正が難しい。
・ 基板洗浄がしにくい。(洗浄は必需ではないですが、ハンダ不良箇所を発見しやすくなります)
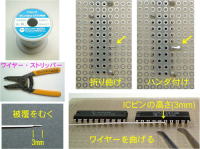
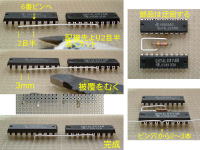 |
そこで、部品面での配線の基本です。
@ 使用するワイヤーは、「ジュンフロン ETFE電線 AWG30 導体径 0.26m/m」で、ユニバーサル基板やラッピング用の単線です。
A 被覆は、必ず電線に対応した、ワイヤー・ストリッパーで、約3mmむきます。
B 接続したい部品の、ピン横の穴にワイヤーを通し、ハンダ面で折り曲げてハンダ付けします。
C ワイヤーを、ICピンの高さ(約3mm)で90°に折り曲げます。
(取り外す際に、つまみやすくするため)
D ワイヤーを、配線先のピン位置より、2.54mm穴換算で、「2目半」長くカットします。
E 被覆を、約3mmむきます。
F ワイヤーを、配線先のピン横の穴に通し、ハンダ面で折り曲げてハンダ付けします。
G ワイヤーの角度を整えて、完成です。
|
配線経路に、抵抗などの部品がある場合は、できるだけ迂回をして配線する方が、部品の値を確認したり、部品を取り換える際に有効です。
実装密度が高く、ピン横に穴を確保できない場合や、プリント基板などの場合は、ワイヤーが単線なので、ICのピンなどに直接ワイヤーを2〜3本差し込むこともできます。
|
10.基板ハンダ面の洗浄 |
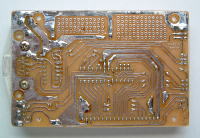
↓
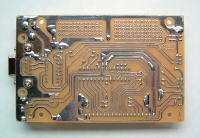 |
私が使用しているハンダのヤニは、非塩素系なので、あえて洗浄の必要はありませんが、洗浄することによって、ハンダのつのや、ハンダ玉の飛び散り等の、ハンダ付け不良が発見しやすくなります。
また、ヤニは経年変化で劣化して、見た目も汚くなるので、洗浄を行っています。
洗浄剤は、サンハヤトからも販売されていますが、機材の掃除などに、無水エタノールを良く使用するので、これで基板の洗浄も行っています。
「無水エタノール」は、薬局で消毒用の物が、500mLで1,000円〜1,500円で入手できます。
|
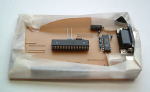
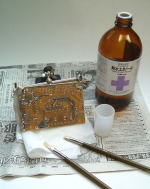 |
まず、部品面にエタノールがかからないように、塗装用のマスキングテープで保護します。
基板を斜めに立てかけて、下にティッシュペーパーを敷き、堅めの図画用の絵筆で、ハンダヤニをこすっていきます。
(絵筆の先を、5mmほどに切りそろえると便利です)
ヤニが多い場合は、ティッシュペーパーで吸い取りながら進めて下さい。
最後に柔らかい筆で、エタノールを流しかけて完了です。
ユニバーサル基板の場合は、未使用の穴もすべてハンダで埋めておくと、部品面が汚れなくなります。
注、換気には十分注意してください! |
|
11.結束線の結び方 |
・ケース内の配線や、ユニバーサル基板の配線などは、信号レベルごとに束ねておくと、ハンダ付け 部分へのストレスや、線材自身の金属疲労も少なくできる上に、見た目も美しくなります。
・配線を束ねる材料は、真空管時代に「モノヒラメント」と呼ばれた凧糸を使用していましたが、今は、ビニール製の結束線が、600円程度で入手できます。
結び方は、ロープワークで言う「クローブ・ヒッチ(クラブヒッチ)」です。
紐の通し方によって、数通りの方法が可能ですが、写真では基板上の配線を束ねる際に、左手で結束線を持ち、右手でピンセットにより結束線を引き出す手順によるものです。
束ねる信号線の内容によっては、干渉をおこす場合がありますので注意して下さい。
また、強く束ねすぎると、ワイヤーの被覆にもダメージがありますので、注意して下さい。
他の通し方は、「クローブ・ヒッチ(クラブヒッチ)」で検索すると、見つかります。
|
12.収縮チューブ |
・収縮チューブは、熱を加えることにより収縮し、部品や端子の形状に合った形に変形するので、ビニールテープなどによる絶縁より確実で、大変便利な材料です。
製品名では、「スミチューブ」住友電工製、「ヒシチューブ」三菱樹脂製とも呼ばれ、透明や黒などの色付きの物もありますが、私は収縮後もハンダ付けの状態が見える、透明を好んで使用しています。
熱を加えるには、ヘヤードライヤーよりも数倍高温の風が出る、「ヒートガン」(工業用ドライヤー)を使用します。
価格は約8,000円〜と高めで、車関連の作業にも使われるため、ホームセンターでも購入できます。
写真のように、ピンコネクターにワイヤーを取り付ける場合、ハンダ付けをしたままでは、コネクターの抜き差しでハンダ付け部分が金属疲労をおこし、切れてしまうことがありますが、収縮チューブで加工することにより、ワイヤーが固定されるため、丈夫になります。
特にAC100V電源などの高圧部分は、試験中の感電やショートによる破損を防ぐために、必ずチューブをかけておくと良いでしょう。
ヒートガンは、500°近い熱風が出るので、火傷や温めすぎによる部品の破損・変形には、くれぐれも注意して下さい。
また、熱風で使用後、すぐにスイッチを切ると、ヒーターが高温になりすぎて切れてしまうので、風の温度が下がるまで冷風にして冷やして下さい。
|
13.シールド線の末端処理 |
・シールド線には、編組タイプ(編み線)やアルミラップタイプがありますが、どちらもコネクターや基板に直接ハンダ付けする際には、下記のような難点があります。
・シールド部分が裸なので、チューブやテープで絶縁する必要がある。
・シールド線がハンダを吸って堅くなり、折り曲げができず自由がきかない。
・シールド線が太いので、基板の穴に入りにくい。
・シールド部分のハンダ付けの際に、熱が絶縁体に伝わりやすく、溶けてしまうことがある。
上記の問題を解決するために、シールド部分にも、リード線を付けるのが得策です。
これにより、コネクターや基板への取り付けが、簡単で確実に行えます。
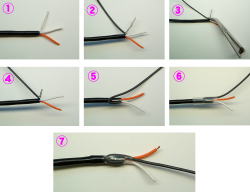 |
@ シールド部分を束ねる。
A シールド部分に、リード線を撚り(より)付ける。
B ヒートクリップで放熱しながら、ハンダ付けをする。
C
5mmほどの長さにカットする。
D ハンダ付け部分を折り返し、リード線で
取り巻く形に加工する。
(ハンダ付け部分の金属疲労防止のため)
E 収縮チューブを被せて、熱処理する。
(テーピングも可)
F 完成。 |
|
14.スペーサー(支柱)の自作 |
・グラフィックLCD 「SG12232C」等の取り付けネジは、2.5mm穴になっており、マザー基板やケースに取り付ける際に、市販のM3(3mm)ネジ用のスペーサー(支柱)が使えません。
また、端子のピンヘッダーとピンソケットの厚みが11mmと変則で、パーツ店では、対応できるスペーサー(支柱)が入手しづらいと思います。
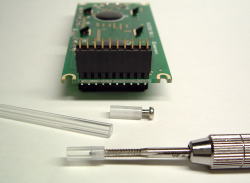
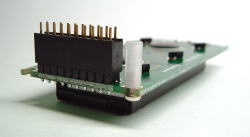 |
そこで、このスペーサー(支柱)を、簡単に自作します。
ホームセンターで、ABS樹脂の4mm丸パイプを購入し、長さ11mmに切りそろえます。
(カッターの刃を立てて、転がしながら切れます)
2.6mmタップで、両側から中心付近まで、ねじ山を切ります。
これで、自由な長さのスペーサー(支柱)を作ることができます。
素材がABS樹脂なので、強くねじを締め付けると、ねじ山がつぶれますので注意して下さい。
ネジのゆるみが気になる場合は、ネジロック(スリーボンド1401B)等で固定します。
|
◎ 製作が難しい場合は、頒布室にて部品頒布しております。
● 基板・部品の頒布室 ●
|
15.フラットケーブルコネクターの加工 |
・フラット ケーブル コネクターは、たくさんのピン端子の接続に便利ですが、入手するには、専門のパーツ店で専用の圧着器を使い、加工してもらう必要があります。
・しかし、通販では加工品を入手しにくいことや、専門のパーツ店を訪れるのも手間な事です。
・そこで、このフラットケーブルコネクターを、アマチュア用に自宅で加工する方法です。
・コネクター自体は、20ピンが200円程度で購入できます。
(ヒロセ製のHIF3タイプは、3点で1セットです)
http://www.hirose.co.jp/products/HIF3B_1.htm
・フラットケーブルも、ジャンクショップ等で、パソコンのIDEハードディスク用の40ピンケーブルが、安く手に入ります。
・これを、必要な長さとピン数に切り分けて使用します。
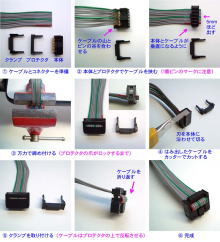 |
@ ケーブルとコネクターを準備します。
A 本体とプロテクタの間に、ケーブルの山とピンの
谷を合わて、本体とケーブルが垂直になるように
はさみます。
・1番ピンのマーク▲と、ケーブルの1番を合わせて下さい。
・本体から、ケーブルを5mmほど出しておいて下さい。
・本体のスリット(突起)方向と、ケーブルが引き出される方向に注意して下さい。
・ケーブルは、圧着したときと反対方向に引き出されます。
・プロテクタもクランプも、一度取り付けると外せなく
なるので、良く確認してから取り付けて下さい。
B 本体とプロテクタを万力ではさみ、プロテクタの
爪がロックするまで締め付けて下さい。
C 本体からはみ出したケーブルを、カッターの刃を
本体に沿わせて、カットして下さい。
D ケーブルをプロテクタの上で折り返して、クランプを
取り付けて下さい。
E
これで完成です。
|
・この方法では、万力の大きさにもよりますが、34ピンまでが圧着の限度のようです。
|
16.ケース加工 空き缶も工具に? |
・ケース加工の道具
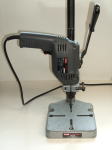 |
ドリル
ハンドドリルでは、なかなかきれいな加工が望めないので、電気ドリルをお勧めします。
回転速度が変えられる変速タイプであれば、アルミやアクリルなどの素材に合わせて加工ができます。
(アクリルやプラスチックは、回転数が高いと摩擦熱で穴の周囲が溶けてしまいます)
また、ドリルスタンドがあると、穴あけのブレを防いだり、垂直に穴があけられます。
|
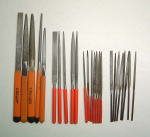 |
ヤスリ
私も、ヤスリは各種たくさん用意しています。
加工部分の形状や大きさに合わせてヤスリを使い分けることで、きれいな加工ができます。
手間はかかりますが、荒削りから仕上げへと、段階を分けて加工することが重要です。 |
 |
スコヤと円定規
スコヤは電子工作になじみが薄いかもしれませんが、ケース加工には必需品です。
ケースの辺に対して、直角のラインが簡単に引けます。
ケース加工では、円の罫描の際にコンパスが使いにくいので、円定規が便利です。 |
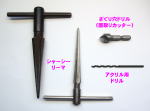 |
シャーシーリーマ
3〜10mm程度のドリル穴をあけ、その穴を20mm程度まで広げられます。
ざぐり穴ドリル (面取りカッター)
穴のバリを取ったり、皿ネジ用の谷穴を加工します。
(刃のタイプや枚数・サイズにより、色々な種類があります)
アクリル用ドリル
アクリル専用のドリルは、先端が特殊な形状になっており、アクリルの割れを防ぐことができます。
|
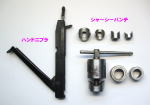 |
ハンドニブラ
ハンドニブラは、大きな角穴や窓穴をあける時に使用します。
先端が貫通する程度(約10mm)の穴をあけ、ハンドルを1回握ると2〜3mmずつ切り進むことができます。
(穴が大きいと、握る回数も多くなり結構疲れますので、下記のドリル穴を連ねる方法がお勧めです)
シャーシーパンチ
15〜30mmの穴(規定寸)をあける場合は、シャーシーリーマよりも楽できれいな加工ができます。
|
・窓穴の加工
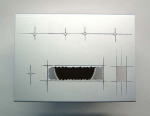
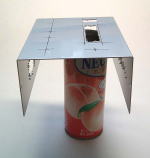 |
アルミケースに、液晶ディスプレイ等の大きな窓を開ける場合、フライス盤のような高価な機械があれば、簡単できれいな仕上がりになりますが、アマチュアには高嶺の花です。
ハンドニブラやドリル穴を連ねて内のりの穴をあけ、ヤスリで仕上げていく作業が一般的ではないかと思います。
しかし、アルミケースにヤスリをかける場合、穴が大きくなるとアルミがしなって作業がしにくくなります。
そんな時、飲み口を缶切りで開けた空き缶が役に立ちます。
空き缶の上で削ることで、アルミ板がブカブカしないのと、削り粉が缶の中に落ちて掃除が楽になります。
直接空き缶にケースを乗せると、ケース内側に傷が付きますから、マスキングテープなどで保護して作業して下さい。
|
・ケース加工の手順
|
17.ブレッドボード用、AVR書込器 ISPケーブル |
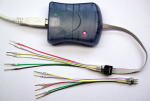
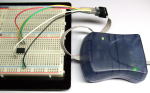 |
ブレッドボード上でAVRマイコンに書き込みを行うための、ISP→先バラピン変換ケーブルです。
6ピンのピンヘッダにケーブルを付け、先端にテストピンを付けてあります。
ショートがないように、収縮チューブで絶縁します。
テストピンの方に端子名シールを貼っておくと、とても便利です!
|
|
18.ジャンパー線の折り曲げ器 |
・基板に使用するジャンパー線は、ピンセットや先端の細いペンチで作っていましたが、数が多くなると、なかなか長さがそろいません。
・市販のリードベンダーでは、折り曲げた際にメッキ線の中央が曲がってしまいます。
・そこで、ジャンパー線専用の折り曲げ器を作りました。
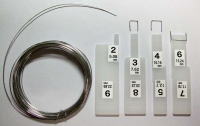 |
3mmのアクリル板を穴ピッチ(2.54mm)ごとに用意して、穴幅で削りながら微妙な寸法を合わせました。
アクリル表面に、フライス盤で0.6mmの溝を入れてあります。
メッキ線を溝に合わせて両側から曲げるだけで、簡単にジャンパー線が出来上がります!
|
・ピンセットで曲げていたのがウソのように効率がよく、 仕上がりもそろいます!
|
|