必要なパーツは次の通り。
大型のホームセンターならば、全てサクッと揃ってしまう材料ばかりです。
・土台となる板(450x60x12mm、\210)
・金属製のパイプ(私は直径16mm、長さ300mmの熱伝導性の高いアルミパイプを使用、\230)
・パイプ用の横受×2コ(内径16mm、パイプの固定が目的なので片空き、\190x2)
・ニクロム線(ダイソーの0.27mm、\105)
・シリコンガラスチューブ(ニクロムとパイプの絶縁目的、内径3mmのものを使用、\315)
・あとは必要に応じて木ネジ、電線等...
もともと持っていたパーツ類を料金に含めても、\1,500程度でしょう。
土台の板などは端材(\0)でも作れますし、\1,000以下に抑えることもできそうです。
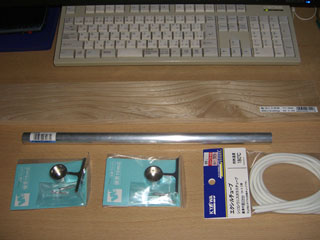
ちなみに、シリコンガラスチューブだけは置いている店が少ないようです。
近所の大型ホームセンター(カインズホーム、スーパービバホーム)では店員に尋ねるも無いとの回答。
なかば店頭での入手を諦めていたところ、ジョイフル本田の瑞穂店でようやく発見。
ここは他ではあまり見ない製品も扱っているので助かります。
ニクロム線は100W〜600Wの品が、安いところでは80円台からホームセンターで売られていますが、今回使う材料によっては計算通りにはいかないでしょうし、温度調整が手探りになることは必至。
ということで、ダイソーで売られている太さ0.27mm×長さ4mの105円のニクロム線を選択。
なんでダイソーでニクロム線が売られているのかはわかりませんが助かります。
あと一つ、抜けているものがあります。
電源。
曲げヒーターを自作される方はAC100Vの直取りをしますが、幼少時代にコンセントで感電を経験してからというもの、AC100Vの直利用は極端に慎重になっているので高出力ACアダプタを使います。
丁度良いものが手元にありました。
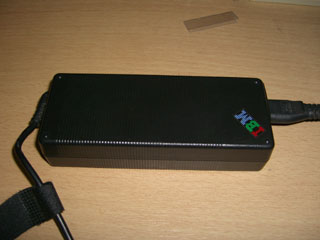
IBMのノートパソコン「ThinkPad R30」で使用していたもので、16V/4.5Aと高出力です。
基本的にノートパソコンはメーカーを問わず高出力のアダプタを利用していることが多いです。
本来の用途外での使用はあまり薦められませんが、貧乏性なので、使える物があれば使います。
|