バキュームフォーム、思ったより反響があってビックリしてます
で、皆さんから色々と質問も受けました
それらの事も盛り込んで実践編を作ってみました
私が考えるにバキュームの大事なファクターは二つあると思います
第一に「型」、次に「火加減」です
そこで、今回はまず"型"について考えます
|
型を作る場合、材質はさして問題ではないです
要は熱で変形しない素材であればなんでも使えます
私は既に書いたように「バルサ材」、そして「ポリパテ」を主に使用しています
|
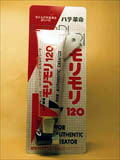 |
問題なのはコレ!
いわゆる「抜け勾配」というヤツです
一般の皆さんには耳慣れない言葉かもしれないですね
要するにバキュームした後でプラ板等から型を引き抜く為に
型にあらかじめ抜けやすい様に勾配を付けておく、と言う事です
というか、これを付けておかないと絶対に抜けません(~_~;
例として「キングカイザーぷち」のランドセルの木型を使って説明します
|
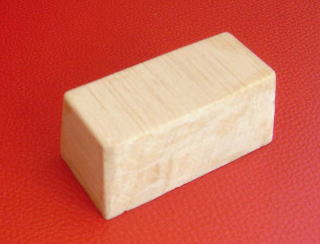 |
これを横から見たところがコレです
上の写真ではタダの直方体に見えますが...
実際には、このように抜け勾配がつけてあります
|
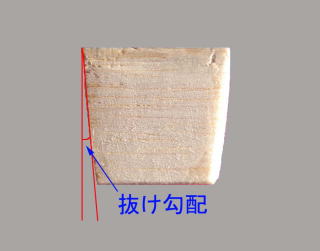 |
当然四面とも付けてあります
|
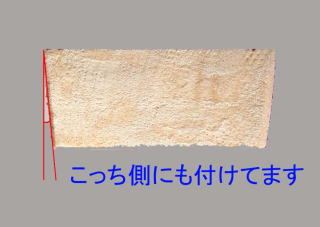 |
この木型で作ったのがコレです
ランドセル(バックパック)は転倒時に力が加わる為
強度が欲しいので1.2mmのプラ板で作りました |
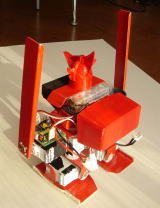 |
前回ご紹介した足の木型ではデザインの段階で「抜け勾配」が考慮されています
どこが「抜け勾配」になっているのか、写真を見て考えてみて下さい |
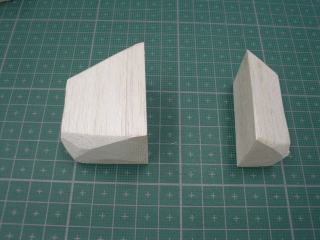 |
では、次に「火加減」について考えます
しかし火力の調節は電気コンロの場合2種類の切替えくらいしかありませんので
正確にいうと「加熱時間」という事になるのでしょうか?
これは熱せられている樹脂板の状態を見て判断するしかありません
そして、どこで加熱を止め、型に押し付けるか? は経験で得るしかありません
と、言ってしまうとミもフタもないですね(~_~;
私の経験から表現するとすれば
熱を加えだすと、樹脂板がフニャフニャになってきます
そして、「溶けて垂れ落ちる寸前」が頃合です
これは文章で表現するのは非常に難しいので何度もやってコツをつかんで下さい
もうしわけないのですが、瞬間の作業なので写真はありません
|
また、BBSの書き込みにも質問がありましたが、掃除機のスイッチを入れる
タイミングは、私の場合は樹脂板を型に押し付ける前です
これは人それぞれで、使用する樹脂板の種類にもよると思います
私が主に使用しているプラ板1.2mmではこうしないとうまく行きません
また、「掃除機の吸引の強さ」ですが、市販の500wのものを
使用していますが、出力目盛りは約80〜90%といったところです
吸引が強すぎると成型品に穴が空いてしまいます
しかし、これはバキュームフォーマーの開口率とも関係します
私の用に魚を焼く網のようなものは開口率が大きすぎるので
掃除機の目盛り(吸引)は弱めです
実際には市販品の用にパンチングメタル(高価ですが)を使用するのが良いと思います |
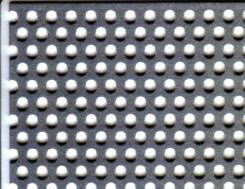 |
また、事前に考慮しておく問題としては成型品(完成品)の厚さです
私の経験では、プラ版の場合バキュームをすると約10〜30%薄くなります
つまり1.0mmのプラ版で作ると完成品は0.7mmくらいになるわけです
設計段階でそれらを織り込んでおかなければなりません |
|
もう少し、この厚さの変化に対して考察してみます
特に薄くなるのは模型の縦方向の面です
これは平面の板を型に押し付けて縦方向に伸ばしてしまうわけですから当然ですね
これに対し、横方向の面の厚さにはほとんど変化がありません
先の例の作例(バックパック)を見てください
これは単純な直方体に近いですのでわかりやすく変化が現れています |
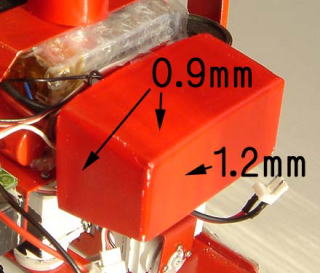 |
この場合はロボットの転倒時に縦に力が加わる部分は肉厚が薄く
平面に力が加わる部分は肉厚が厚くなっていますので、まずまずと言えます |
|
ただ、どうしても設計と製造上の問題で意図しない場所が薄くなって
しまうことがあります。この場合は諦めるしかないのでしょうか?
いえ、やり方によっては縦方向の肉厚変動を少しでも抑えることが
出来ると思います
要はキャスティングにおける溶湯補給の原理を使います
難しい話は置いておいて実際のやり方を解説しましょう
結論だけ先に言います
「型に押し付ける部分を中心になるべく広い範囲を温める」
もう1つ
「材料をケチるな!
樹脂板は型に対して十分大きいものを使う」
以下の説明は興味のある人だけ読んでください
読まなくても全然大丈夫です(~_~;
|
|
バキュームフォームされる樹脂板は型の回りのやわらかくなった部分が
型の形状に沿って伸ばされます
原理的には、型を上から見て製図で言うところの三面図の1つだけを
考えるのではなく、展開図分の面積の樹脂板が必要になるわけです
しかし、実際の作業にあたっては、つい型を上から見た部分の面積(三面図の1つ)
範囲だけをあぶりがち(熱する)になります
これでは暖める面積が足りません
当然、熱っせられてフニャフニャになった部分しか伸びませんので
伸縮する部分の面積が少ないために
盛大に肉厚変動が起きます
これを防ぐために、最低でも展開図分の面積を温める必要があります
これが一つ目のノウハウ
|